others
Understanding Hypoid Gears: The Hidden Power Behind Smooth Torque Transmission
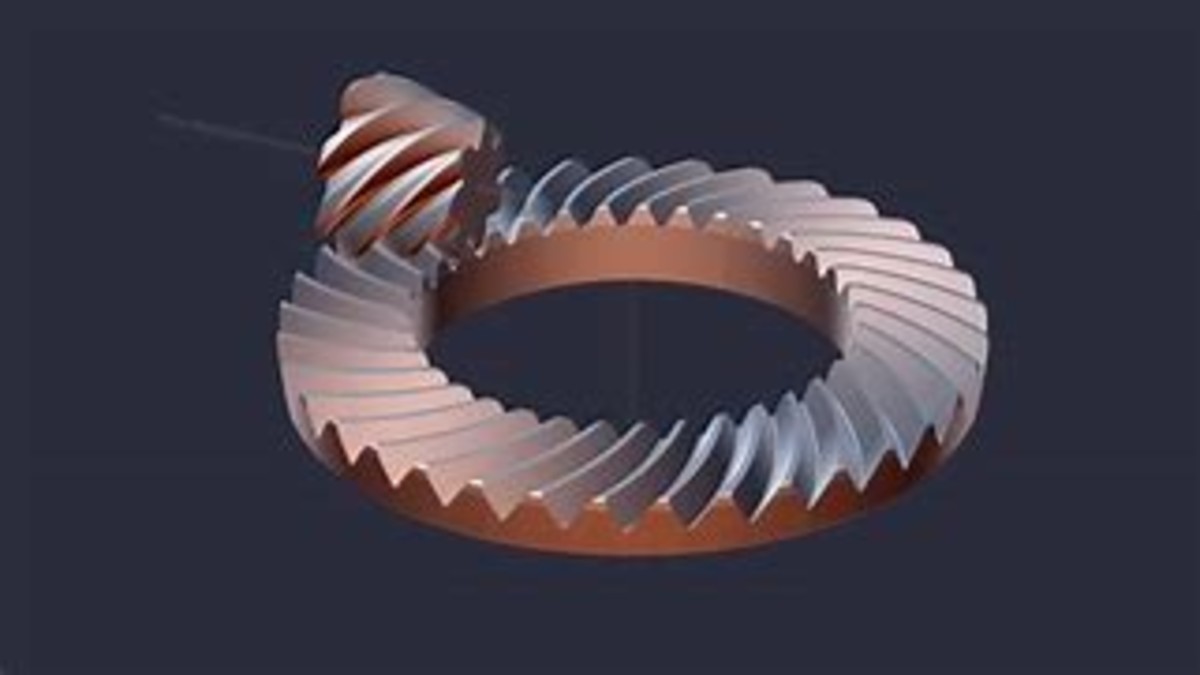
What Is a Hypoid Gear?
A hypoid gear is a type of spiral bevel gear that allows for non-intersecting shaft arrangements meaning the shafts are offset and don’t meet at a point like typical bevel gears. This unique setup allows the gear teeth to slide across each other, providing smoother and quieter operation. First introduced in automotive differentials, hypoid gears have since expanded into other heavy-duty applications.
Hypoid Gears vs. Bevel Gears
At first glance, hypoid and bevel gears look similar. But the magic lies in the offset design. Bevel gears have intersecting axes, while hypoid gears have shafts that are offset vertically, giving them an advantage in torque transmission and smoothness. Hypoid gears also allow for larger pinion diameters, which leads to increased strength and durability.
How Hypoid Gears Work
The gears in a hypoid system engage at an angle, and because of the sliding contact between the pinion and ring gear, they distribute load more evenly. This reduces vibration and noise, especially at high speeds. The offset also means the drive shaft can be mounted lower, making them ideal for automotive use.
Key Components of a Hypoid Gear System
- Pinion Gear: Connects to the input shaft and transmits motion to the ring gear.
- Ring Gear: A larger gear that meshes with the pinion to rotate the output shaft.
- Housing: Encases and aligns the gear set.
- Lubrication System: Reduces friction and prevents wear.
Advantages of Hypoid Gears
- Smooth and Quiet Operation: Thanks to the sliding action.
- Higher Torque Output: Excellent for high-load applications.
- Compact Design: The offset allows for tighter installations, especially in vehicle drivetrains.
Common Applications of Hypoid Gears
Automotive Differentials
This is their most iconic use. Hypoid gears enable better torque delivery to the wheels while allowing for a lower vehicle floor height.
Industrial Machinery
Used in heavy-duty gearboxes and conveyors, where reliability is key.
Aerospace Engineering
Provides reliable torque transfer in space-limited, high-performance environments.
Design Considerations
When designing with hypoid gears, engineers must consider:
- Load and Speed: Determines material and size.
- Gear Ratio: Must match the system’s torque and speed requirements.
- Lubrication: Critical due to the sliding contact.
Materials Used in Hypoid Gears
Most hypoid gears are made from case-hardened steel to withstand heavy stress. Advanced applications may use composite materials for lighter weight without compromising strength.
Lubrication and Maintenance
Lubrication is non-negotiable. Hypoid gears generate more heat due to sliding motion, so they need high-quality gear oil. Synthetic oils with extreme pressure additives are often recommended.
Maintenance Tips
- Regularly check oil levels and quality.
- Replace oil at manufacturer-recommended intervals.
- Inspect gear teeth for wear or pitting.
Efficiency and Performance
Although hypoid gears are not as mechanically efficient as straight-cut gears due to sliding friction, their ability to handle more torque outweighs the efficiency loss in most cases. Plus, innovations in gear oil have closed this gap significantly.
Challenges in Manufacturing Hypoid Gears
Precision is everything. The offset and angle of the teeth make hypoid gears harder to manufacture than traditional gears. Specialized CNC equipment and high-tolerance measurements are required, which increases production costs.
Innovations in Hypoid Gear Technology
Modern advancements are reshaping hypoid gear design:
- CNC Machining ensures high-precision teeth profiles.
- Noise Reduction Coatings help make these gears even quieter.
- Eco-Friendly Lubricants are becoming standard, especially in automotive applications.
Choosing the Right Hypoid Gear System
Selecting the right gear involves evaluating:
- Load Requirements
- Space Constraints
- Speed Demands
Working with an experienced gear engineer or manufacturer ensures optimal performance and longevity.
Future of Hypoid Gears
What’s next for hypoid gears? Expect big things like:
- AI for Predictive Maintenance: Spotting wear before failure.
- 3D Printing for Prototyping: Reducing design cycles.
- Improved Composite Materials: For lighter yet stronger gears.
Final Thoughts
Hypoid gears might not get as much spotlight as other components, but they play a vital role in torque-heavy, high-performance systems. Their unique design offers unmatched benefits in smoothness, strength, and compactness—making them an indispensable part of modern engineering.
FAQs
1. What makes hypoid gears better than bevel gears?
They offer quieter operation, better torque handling, and flexible mounting due to the offset shaft design.
2. Are hypoid gears only used in vehicles?
Not at all. They’re also found in industrial gearboxes, aerospace systems, and power tools.
3. How often should hypoid gear oil be changed?
Typically every 30,000 to 50,000 miles for automotive use, but always follow the manufacturer’s guidelines.
4. Can hypoid gears be 3D printed?
Yes, especially for prototyping, although production gears still rely on machining for durability.
5. What’s the biggest challenge with hypoid gears?
Manufacturing precision. Even tiny errors in angle or alignment can lead to inefficiency or failure.
- entertainment2 months ago
OnionFlix: Everything You Need to Know About This Streaming Website
- others2 months ago
Nook vs Kindle: Which E-Reader Is Right for You?
- food1 month ago
The Ultimate Guide to Salchicha: Everything You Need to Know
- education2 months ago
Why Did My Period Come Early? Understanding Unexpected Menstrual Changes